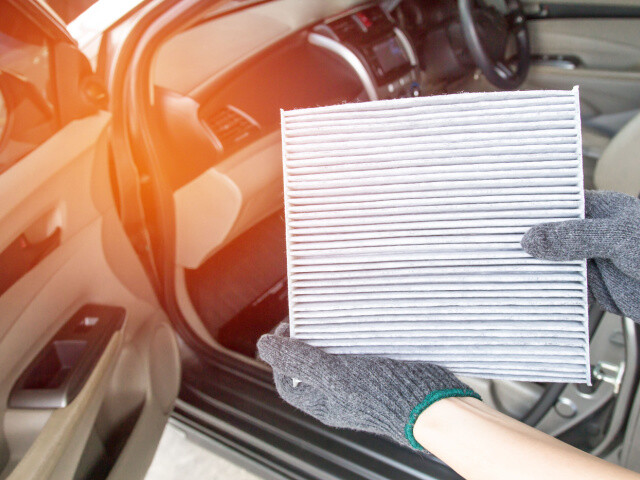
Learn why manufacturers are relying on formulated polyolefin hot melt adhesive solutions for air filtration media applications.
In recent years, manufacturers in the automotive cabin air filter market have been reevaluating how they source the necessary materials to complete finished products for their end-users, including their bonding solutions.
Supply chain shortages have caused many to reconsider what’s most important to them. As a result, they’ve faced challenges in achieving:
Supply chain shortages have caused many to reconsider what’s most important to them. As a result, they’ve faced challenges in achieving:
- High technology performance
- Production line efficiencies
Challenge #1: Achieving High Technology Performance
Supply chain shortages are affecting the ways many manufacturers source bonding materials for air cabin filters. Additional sourcing delays can greatly impact whether manufacturers decide to purchase quality materials they typically rely on for their processes, or if they need to consider something they know they can receive on time. This, however, may cause them to downgrade on the end-use performance if their bonding solution does not include all the necessary capabilities their application requires.
By considering a formulated adhesive technology, it’s possible for manufacturers to ensure they’re receiving the same performance they rely on without the hassle of finding the right materials themselves. This is because a formulated technology will comprise of readily available chemistries and not include materials currently experiencing supply shortages.
How the Right Adhesive Technology Addresses Material Sourcing
By considering a formulated adhesive technology, it’s possible for manufacturers to ensure they’re receiving the same performance they rely on without the hassle of finding the right materials themselves. This is because a formulated technology will comprise of readily available chemistries and not include materials currently experiencing supply shortages.How Polyolefin Hot Melt Adhesives Provide High Technology Performance
As a thermoplastic hot melt adhesive with polyolefin technology, this bonding solution is solid at room temperature, liquifies upon heating and re-solidifies during the cooling process. Polyolefin hot melt adhesives are a common solution in cabin air filter assembly because the polymers offer a range of benefits:- Excellent heat resistance: With a high melting point range of 200° F to 300° F (93.3° C to 148.9° C), hot melt polyolefins provide bonding strength for demanding environments. Specifically, it can withstand high temperatures inside a vehicle without softening and affecting the filter’s overall performance.
- Optimized viscosity: Formulated with tackifiers, polyolefin hot melt adhesives have additives that improve the viscosity to enable strong bonding. Additionally, this provides strong vertical assembly so the adhesive will not creep down a filter’s pleating over time.
- Controlled stabilization: Since polyolefin hot melt adhesives can adhere to a variety of substrates including plastics, metal and paper, it is useful for numerous filtration media types including pleat separation, and media, frame and end cap bonding. This flexible adhesive has the durability to form a protective seal in between the filter cap and pleating, while also providing enough flexibility so it does not crack over time.
Challenge #2: Achieving Production Line Efficiencies
It’s very easy for supply chain disruptions to impact day-to-day operations for a filter manufacturing plant. If a manufacturer is waiting for bonding solutions to complete their air cabin filters, they may be forced to either prepare for increase operations expenses or reconsider production line or worker schedules to keep operation costs down. Further, a filter manufacturer waiting for bonding solutions to complete air cabin filters could play a domino effect in slowing down automotive manufacturers relying on those finished products for their processes.
How the Right Adhesive Technology Addresses Manufacturing Disruptions
With a formulated adhesive technology, manufacturers can gain more control over their own processes while the industry faces supply chain disruptions. Adhesives can be formulated with capabilities that are useful for multiple substrates and end-use applications. This allows the manufacturers to utilize one bonding solution for numerous products, helping them maintain a schedule that involves less downtime.
How Polyolefin Hot Melt Adhesives Provide Production Line Efficiencies
Polyolefin hot melt adhesives enable manufacturers to develop durable air cabin filters at a rate necessary to ensure durability, while also providing capabilities useful for multiple end-use products. This includes:
How the Right Adhesive Technology Addresses Manufacturing Disruptions
With a formulated adhesive technology, manufacturers can gain more control over their own processes while the industry faces supply chain disruptions. Adhesives can be formulated with capabilities that are useful for multiple substrates and end-use applications. This allows the manufacturers to utilize one bonding solution for numerous products, helping them maintain a schedule that involves less downtime.
How Polyolefin Hot Melt Adhesives Provide Production Line Efficiencies
Polyolefin hot melt adhesives enable manufacturers to develop durable air cabin filters at a rate necessary to ensure durability, while also providing capabilities useful for multiple end-use products. This includes:
- Long open time: Polyolefin hot melt adhesives’ high melting point range allows the flexibility for the necessary set up time needed for the filter application. This allows it to be easily incorporated into bead or slot dye extrusion application methods. A manufacturer can easily place down a significant volume of adhesive for a large filter without worrying the adhesive will cure before they complete the required working time.
- Wide processability: Formulated with good thermal stability, polyolefin hot melt adhesives can adhere to multiple substrates such as paper, plastic and metal. This provides a manufacturer the option to use this adhesive technology on multiple filtration media types if desired, helping them complete more production with less changeovers and downtime to stay on schedule.
- Improved Sustainability: Polyolefin hot melt adhesives have both low odor and low VOC formulation, making them non-toxic and often recyclable. This can help improve the overall working environment for facility employees.
How Bostik Can Address Air Cabin Filtration Needs
At Bostik, we understand how challenging it can be for manufacturers to find the bonding solutions they need while supply chain disruptions are taking place. As a global company under Arkema, we provide cost-effective products and flexible formulations that can address key performance needs for specific filtration applications.
Our polyolefin adhesive solutions, based on a range of hot melt technologies, can benefit automotive air cabin filtration bonding needs, allowing for:
Increased performance: Key performance additives with high-temperature resistance to enhance specific filtration end-use needs
Improved processes: Long open times enable necessary manufacturing rates and flexibility to use on multiple substrates
Interested in learning more about polyolefin adhesives? Contact a Bostik representative to find out how this technology can benefit your filtration application.
You can also check out this other useful content to understand filter adhesives:
On-Demand Webinar: Understanding Your Adhesive Needs in Filtration
VIDEO: Improve Filter Manufacturing
Why You Need Polyamide Adhesives for Filter Manufacturing
Our polyolefin adhesive solutions, based on a range of hot melt technologies, can benefit automotive air cabin filtration bonding needs, allowing for:
Increased performance: Key performance additives with high-temperature resistance to enhance specific filtration end-use needs
Improved processes: Long open times enable necessary manufacturing rates and flexibility to use on multiple substrates
Interested in learning more about polyolefin adhesives? Contact a Bostik representative to find out how this technology can benefit your filtration application.
You can also check out this other useful content to understand filter adhesives:
On-Demand Webinar: Understanding Your Adhesive Needs in Filtration
VIDEO: Improve Filter Manufacturing
Why You Need Polyamide Adhesives for Filter Manufacturing
©2023 Bostik, Inc. All Rights Reserved
All information contained herein is believed to be accurate as of the date of publication, is provided “as-is” and is subject to change without notice. To review our full U.S. Legal Disclaimer, visit: https://bostik.com/us/en_US/privacy-policy/legal-disclaimer
All information contained herein is believed to be accurate as of the date of publication, is provided “as-is” and is subject to change without notice. To review our full U.S. Legal Disclaimer, visit: https://bostik.com/us/en_US/privacy-policy/legal-disclaimer