Jan 12, 2024 - 3-5 minutes
Overcome Manufacturing Challenges with Low Pressure Molding Adhesives
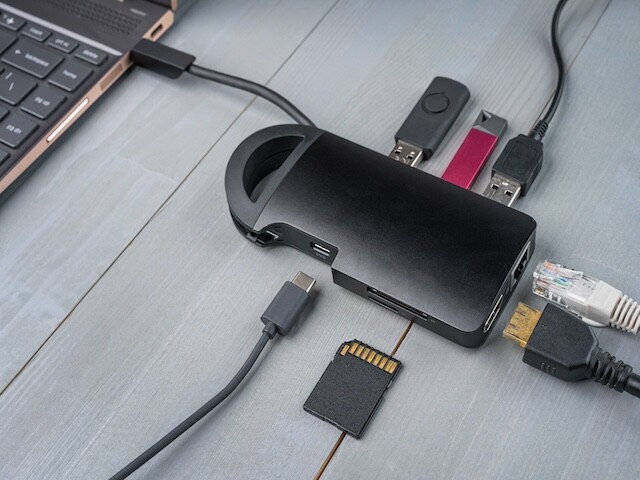
Learn how low pressure molding (LPM) can protect electronic devices from environmental elements while enhancing processing efficiencies. Find out about the limitations of conformal coating, potting, and high-pressure molding, and find out how LPM offers a sustainable, cost-effective solution.
When manufacturing electronic devices, it’s important to encapsulate, seal, and protect delicate parts from elements including dust, water, and UV exposure for a long lifespan. However, traditional methods such as conformal coating, potting, and high-pressure molding may not always provide the right application to accomplish these goals. Find out why these methods may not be providing the end-use performance you need and what adhesive solution can overcome these challenges.
#1: Conformal Coating Limitations
Conformal coating provides a thin, protective polymeric layer to electronic parts and circuit boards, preventing moisture, dust, chemicals, or other environmental factors from affecting the inside components. However, it does not always serve as the most efficient method to safeguarding electronics.
Coating difficulties:
Electronic assemblies often contain a variety of components with different shapes, sizes, and orientations. Therefore, achieving consistent conformal coating thickness across all components can be challenging, leading to variations and even defects in the coating. These imperfections can lead to air entrapment, coating bridging, or incomplete coverage, resulting in a lack of protection for the internal electronic components. It can also be difficult to remove conformal coating from a fragile internal component that needs to be repaired or replaced, which can lead to complexities or extended downtime to avoid additional damage.
Minimal thermal management:
Conformal coating often serves as an insulator, which can lead to poor thermal conductivity. Important applications such as wearable electronics or automotive sensors may not be capable of providing the efficient thermal management levels, which could cause inconsistencies in the overall product performance.
Rigidity:
While conformal coating is compatible with connectors, metals, plastics, glass, and printed circuit boards (PCBs), it can lack flexibility to provide load-bearing during mechanical stress if thick coat weights are used or rigid additives for structural strength are in the coating formulation. This could result in the coating cracking or delaminating. Further, if the conformal coating has a different coefficient of thermal expansion than the substrate, stress or cracking can also occur.
#2: Potting Limitations
Placing an electronic component in a mold and filling it with potting compound is considered a classic solution to protecting electronic components. However, there are some factors that might not make it the most suitable option:
Hazardous materials:
Potting compound typically includes hazardous materials such as isocyanates, which are in two-part polyurethanes (2K PURs) commonly used in the formulation. This may cause concern in applications where environmental regulations play a factor.
Processing complexities:
As mentioned above, potting compound may be comprised of a two-component technology, which can require mixing. This increases the chances of errors likelihood, which will require additional downtime to correct. Potting compound also requires at least 24 hours to cure due to crosslinking or polymerization and temperature factors, which can increase production time or result in utilizing additional equipment to keep processes moving.
Added Weight and Size:
Since potting compound fills the mold as one of the last assembly steps, it adds weight to the end-use product. This additional weight can potentially increase the carbon footprint if the electronic application especially if used in automotive or other transportation vehicles and runs counter to the lightweighting trend to save on fuel consumption. Further, in compact designs, the added volume of the potting compound may not be feasible since it will increase the product’s overall size.
#3: High Pressure Molding (HPM)
High pressure molding (HPM), which includes injection and compression molding processes, is commonly used for producing plastic or metal electrical components. However, there are some factors that may not make it suitable:
Delicate material distortion:
The pressure applied during molding can place mechanical stress that may be too overwhelming to delicate materials such as semiconductors and thin film electronics, leading to deformation, cracking, or other damage.
Cost Inefficiencies:
HPM requires heavy, resistance seal mold, which is often cost-effective for high-volume productions because it is distributed more evenly over large units in mass production compared to smaller production batches or testing phases. Further, electronic components with strict requirements, such as microprocessors or sensors, may lead to waste if certain materials are not compatible. It can also be difficult to modify molds as needed due to the complexity and precision required in their design, the need for specialized manufacturing processes, and the potential impact on the structural integrity of the mold. Making changes to the molds therefore can result in additional costs for downtime or materials.
Heat degradation:
For electronic components that are sensitive to heat, HPM temperatures can potentially cause damage or degradation, as it provides a temperature range between 446°F (230°C) and 572°F (300°C). These high temperatures tend to melt and solder joints and destroy connections.
How Low Pressure Molding (LPM) Overcomes Challenges
Low pressure molding (LPM) is formed from carboxylic diacids and diamines to create polyamide hot melt adhesive solutions, offering strong protection to a variety of electronic components such as plastics, metals, and ceramics while maintaining production efficiencies. With a three-step process that involves both classic injection and resin potting, LPM can overcome key challenges found with conformal coating, potting, and HPM:
Delicate Component Sensitivity:
With low viscosity levels, LPM enables low process pressure, making it suitable for electronic components with delicate structures or sensitive materials. Further, it has a low temperature range of 356°F (180°C) to 446°F (230°C) compared to HPM. This helps minimize thermal damage during manufacturing, especially for electronic components with heat-sensitive elements. At these temperatures, you are also protecting any sensitive solder joints from melting and breaking the circuit.
Ease of Processing:
LPM provides low-temperature, fast cycle times of 90 seconds. Its thermoplastic properties enable it to set rapidly, unlike potting compound. Further, LPM consists of a one-component solution that does not need to be mixed, which eliminates the overall mixing error likelihood and improves convenience. LPM also offers increased cost efficiencies compared to HPM because it utilizes lighter, aluminum seal molds that can be used for small production batches or testing phases. Unlike conformal coating capabilities, LPM also offers flexibility to handle mechanical stress or vibration. The elasticity makes it easier to rework if necessary and prevent cracking or delamination.
Improved Environmental Footprint:
As a solventless solution, LPM can help improve worker safety over traditional solutions such as potting compound. It is also made out of bio-sourced materials, including castor oil and rapeseed that is produced into diacids. LPM has the potential to decrease the weight of a part compared to potting which helps overall sustainability for electronic devices. Light weight parts translate to lower fuel cost for shipping material and lightweighting for vehicles.
How Bostik Can Help
As the adhesives solution segment of Arkema, Bostik is well integrated to provide LPM solutions. Bostik LPM materials are made from up to 80% biosourced materials. Furthermore, the biosourced materials come from plants like the Caster bean or Rape Seed and are taken from segments that do not affect the global food stream.
Contact a Bostik expert to learn how our offerings can protect electronic devices from environmental elements while enhancing processing efficiencies and reducing the environmental footprint.
Other Relevant Content:
Low Pressure Molding Adhesives
Why Polyamide Adhesives in Low Pressure Molding Are Revolutionizing Electronics
Meet Your Goals with the Right Low Pressure Molding (LPM) Method
©2024 Bostik, Inc. All Rights Reserved
All information contained herein is believed to be accurate as of the date of publication, is provided “as-is” and is subject to change without notice. To review our full U.S. Legal Disclaimer, visit: https://bostik.com/us/en_US/privacy-policy/legal-disclaimer