Aug 16, 2023 - 3-5 minutes
How You Can Make a More Effective EV Battery Pack
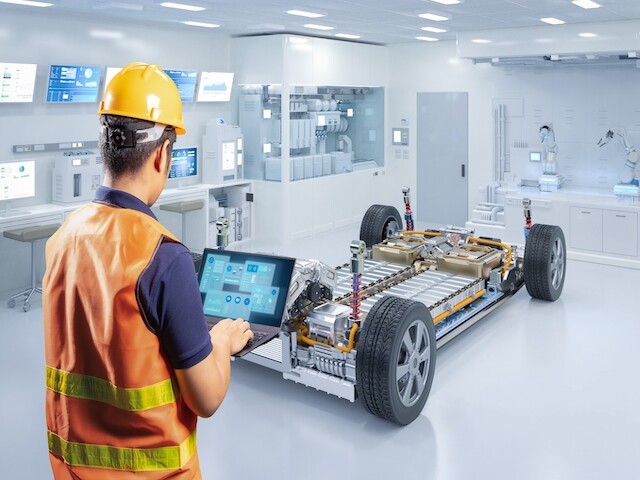
As electric vehicle (EV) demand surges, automotive OEMs focus on optimizing battery packs for longevity and power density. Learn how adhesives contribute to achieving these goals and gain insights into selecting the right adhesive solutions for EV battery packs.
As demand for electric vehicles (EVs) grows, automotive OEMs work to develop increasingly more effective battery packs to enable drivers to get the most out of their EV and environmental impact reduction efforts. To accomplish this, it is critical to stay up-to-date on the latest developments, such as:
- Battery optimization: OEMs want EV battery packs to provide extended longevity, so the end user does not have to replace them often. To do this, it involves learning the best ways to ensure thermal management during in-service and charging processes.
- Power density: OEMS also want EV battery packs to move the power effectively and supply energy to the electric motor. To do this, they must find ways to increase power density to enable fast acceleration, such as through lightweighting.
The Role Adhesives Play in Battery Pack Manufacturing
When thinking about adhesives, consider how they impact both the OEMs during the manufacturing process and the end user when the battery pack is operating in an EV.
Battery Pack Performance
Maintenance serviceability: An adhesive also can help OEMs save on battery pack downtime or repairs. For example, it can be formulated so that it’s easy to open the seal to remove the previous adhesive inside as well as reseal with new adhesive once the internal battery is repaired. Additionally, adhesive plays a role in how often these repairs must take place. For example, when lightweighting occurs, it is common for an EV battery pack to experience vibration amongst the battery cells, which can require more maintenance work to fix it. An adhesive that enables flexibility can help reduce vibration, protect against environmental factors and enhance sound damping within the battery, resulting in fewer overall repairs for the end user throughout the vehicle’s lifespan.
Further, the adhesive’s formulation should be taken into consideration, as it can impact the precautions OEMs must take in their facilities to protect workers during manufacturing. Particularly, adhesives that contain acrylic monomers or flammable solvents can possess strong odors or carcinogens that require proper ventilation systems. These formulations also may pose flammability risks and require proper storage handling for protection.
Battery Pack Sustainability Enhancements
Battery Pack Performance
- Design options: Battery packs are manufactured with different materials, such as nylon and metal. The types of materials an adhesive technology can bond to influence the materials that can be chosen or not, which can impact overall battery pack construction. For example, if an adhesive cannot bond to certain materials and the engineer can’t find an adhesive that can bond to those materials, it limits the engineers’ design options even if the materials would otherwise be beneficial for battery pack construction.
- Battery charge longevity: As mentioned previously, it’s critical for EV battery packs to offer a long lifespan to prevent the end user from replacing them often. Adhesives can help by providing:
- Thermal stability: An adhesive with enhanced thermal management is equipped to handle temperature changes and reduce overheating, which will create less stress on the battery components. This will result in minimized degradation over time and consistent energy storage to extend the overall battery life, enabling the end user to trust that the EV battery will be efficient in both cold and high temperature environments. Additionally, an adhesive can also provide temperature resistance so it will maintain its bond when a battery experiences high temperatures while in use.
- Environmental protection: An adhesive with a strong bond will stop any elements from getting inside the battery that could cause short circuiting, such as dust, moisture or chemicals. This will allow the battery to maintain high power density for fast acceleration, resulting in a reliable electric motor that helps the end user easily take short or long trips.
Maintenance serviceability: An adhesive also can help OEMs save on battery pack downtime or repairs. For example, it can be formulated so that it’s easy to open the seal to remove the previous adhesive inside as well as reseal with new adhesive once the internal battery is repaired. Additionally, adhesive plays a role in how often these repairs must take place. For example, when lightweighting occurs, it is common for an EV battery pack to experience vibration amongst the battery cells, which can require more maintenance work to fix it. An adhesive that enables flexibility can help reduce vibration, protect against environmental factors and enhance sound damping within the battery, resulting in fewer overall repairs for the end user throughout the vehicle’s lifespan.
Further, the adhesive’s formulation should be taken into consideration, as it can impact the precautions OEMs must take in their facilities to protect workers during manufacturing. Particularly, adhesives that contain acrylic monomers or flammable solvents can possess strong odors or carcinogens that require proper ventilation systems. These formulations also may pose flammability risks and require proper storage handling for protection.
Battery Pack Sustainability Enhancements
- Electrical insulation: By utilizing effective electrical insulation techniques, OEMs can design battery packs that are more energy dense to increase the vehicle performance for the end user. To do so, electrically-conductive adhesives help:
- Incorporate thinner insulation separators to prevent short circuits
- Enable high-voltage capabilities while reducing battery cells
- Prevent a charge from spreading out inefficiently
How to Choose the Right Adhesive Technology
While there are a range of adhesive technologies that offer EV battery pack compatibility levels, it's important to understand their different capabilities to aid in making the right selection. For example:
- Acrylic adhesives can bond to many substrates such as metal, plastic, glass and textiles, but OEMs must consider the additional facility requirements they’ll need to address the odor and flammability risks, such as point exhaust systems and ventilation. This may also result in complex regulatory issues.
- Epoxy adhesives can cure at room temperature to protect sensitive battery components that may not react well to heat, but they do not offer high elongation required for expansion and contraction to offset dissimilar substrates. This means the adhesive is more likely to crack or fail when exposed to stresses, potentially compromising the structural integrity of the battery pack. Additionally, the lack of flexibility in can result in fatigued joints from increased vibration.
Unlike acrylic and epoxy adhesives, these technologies provide the necessary capabilities that OEMs need to manufacture battery packs that achieve key goals.
Silyl Modified Polymer (SMP): SMP is similar to acrylic adhesives with compatibilities to metal, plastic, glass and textile substrates, but it also offers primerless adhesion to simplify processes, which is not always the case with acrylic adhesives. Further, unlike acrylic adhesives, SMP can be flame retardant. It also is isocyanate free, eliminating the need for additional ventilation and storage requirements while enhancing work safety.
SMP also provides high elasticity over epoxy adhesives, which helps decrease vibration to enhance the battery’s longevity. While both options include room temperature curing, SMP offers varied open times, rapid strength build during assembly and high elongation, which epoxy adhesives cannot fully provide. This ensures the battery will prevent dust, moisture or chemicals from affecting the dissimilar substrates.
Two-Part Polyurethane Adhesives (2K PUR): Similar to acrylic adhesives, 2K PUR adhesives can bond to multiple substrates such as nylon to aluminum or steel. They can also bond conversion coated aluminum to different steel alloys. However, unlike acrylic adhesives, 2K PUR can offer flame retardancy with no odor. This allows OEMs to use 2K PUR for a variety of substrate needs without the additional precautions to account for flammability risks.
These adhesives also offer more versatility than epoxy adhesives because they offer higher elongation, enabling improved elasticity for thermal expansion. Further, 2K PUR adhesives can cure either with heat or room temperature and maintain adhesion. With the ability to cure at room temperature, OEMs can use 2K PUR on multiple battery components while reducing overall energy usage, helping end users improve their carbon footprint when purchasing an EV.
Reactive Hot Melt Polyurethane (HMPUR): After reactive HMPUR adhesives are heated for application, they react with moisture in the air to crosslink during the cooling process, which creates chemical and environmental resistance. Like acrylic adhesives, this enables reactive HMPUR adhesives to protect demanding applications within the EV battery pack. However, reactive HMPUR adhesives are comprised of 100% solids, making them solvent-free; this means they do not require specialized ventilation and storage like acrylic adhesives do. Reactive HMPUR adhesives develop high green strength and flexibility during the cooling process, allowing them to maintain bonding while improving sound damping and vibration better than rigid epoxy adhesives.
Silyl Modified Polymer (SMP): SMP is similar to acrylic adhesives with compatibilities to metal, plastic, glass and textile substrates, but it also offers primerless adhesion to simplify processes, which is not always the case with acrylic adhesives. Further, unlike acrylic adhesives, SMP can be flame retardant. It also is isocyanate free, eliminating the need for additional ventilation and storage requirements while enhancing work safety.
SMP also provides high elasticity over epoxy adhesives, which helps decrease vibration to enhance the battery’s longevity. While both options include room temperature curing, SMP offers varied open times, rapid strength build during assembly and high elongation, which epoxy adhesives cannot fully provide. This ensures the battery will prevent dust, moisture or chemicals from affecting the dissimilar substrates.
Two-Part Polyurethane Adhesives (2K PUR): Similar to acrylic adhesives, 2K PUR adhesives can bond to multiple substrates such as nylon to aluminum or steel. They can also bond conversion coated aluminum to different steel alloys. However, unlike acrylic adhesives, 2K PUR can offer flame retardancy with no odor. This allows OEMs to use 2K PUR for a variety of substrate needs without the additional precautions to account for flammability risks.
These adhesives also offer more versatility than epoxy adhesives because they offer higher elongation, enabling improved elasticity for thermal expansion. Further, 2K PUR adhesives can cure either with heat or room temperature and maintain adhesion. With the ability to cure at room temperature, OEMs can use 2K PUR on multiple battery components while reducing overall energy usage, helping end users improve their carbon footprint when purchasing an EV.
Reactive Hot Melt Polyurethane (HMPUR): After reactive HMPUR adhesives are heated for application, they react with moisture in the air to crosslink during the cooling process, which creates chemical and environmental resistance. Like acrylic adhesives, this enables reactive HMPUR adhesives to protect demanding applications within the EV battery pack. However, reactive HMPUR adhesives are comprised of 100% solids, making them solvent-free; this means they do not require specialized ventilation and storage like acrylic adhesives do. Reactive HMPUR adhesives develop high green strength and flexibility during the cooling process, allowing them to maintain bonding while improving sound damping and vibration better than rigid epoxy adhesives.
How Bostik Plays a Key Role in EV Battery Pack Manufacturing
As the adhesives division under Arkema, Bostik is dedicated to helping OEMs develop EV battery packs that are comprised of high-quality adhesive solutions to address manufacturing and performance needs.
Our silyl modified polymer (SMP) solutions offer versatility for sealing, bonding and glazing to increase production efficiencies. This option is also 100% isocyanate and solvent-free, helping OEMs enhance the ways they address EV end users’ sustainability interests while maintaining flexibility and high resistance to harsh conditions for a prolonged battery life.
Bostik has been a leading developer in designing a polyurethane adhesive solution that can bond metal and thermoplastic at the same time, helping reduce complexities in bonding multiple components. Further, our two-part, polyurethane adhesives can bond to metal without primers or treatment. This technology also has low-viscosity for precise gravity-flow dispense of beads or continuous coverage streaming, helping OEMs use current equipment to make the most of their adhesive supply.
Additionally, Bostik’s reactive hot melt polyurethane adhesives are specifically designed with low viscosity for precise manual or automatic dispensing, helping OEMs get the most from their adhesive supply. This technology also offers excellent humidity, temperature and impact resistance to protect the battery pack and enhance the lifespan, reducing repairs over time for the end-user.
Looking for an adhesive solution that can enhance the development of EV battery pack manufacturing and performance? Contact a Bostik expert to learn how our adhesive solutions are the right choice.
Our silyl modified polymer (SMP) solutions offer versatility for sealing, bonding and glazing to increase production efficiencies. This option is also 100% isocyanate and solvent-free, helping OEMs enhance the ways they address EV end users’ sustainability interests while maintaining flexibility and high resistance to harsh conditions for a prolonged battery life.
Bostik has been a leading developer in designing a polyurethane adhesive solution that can bond metal and thermoplastic at the same time, helping reduce complexities in bonding multiple components. Further, our two-part, polyurethane adhesives can bond to metal without primers or treatment. This technology also has low-viscosity for precise gravity-flow dispense of beads or continuous coverage streaming, helping OEMs use current equipment to make the most of their adhesive supply.
Additionally, Bostik’s reactive hot melt polyurethane adhesives are specifically designed with low viscosity for precise manual or automatic dispensing, helping OEMs get the most from their adhesive supply. This technology also offers excellent humidity, temperature and impact resistance to protect the battery pack and enhance the lifespan, reducing repairs over time for the end-user.
Looking for an adhesive solution that can enhance the development of EV battery pack manufacturing and performance? Contact a Bostik expert to learn how our adhesive solutions are the right choice.
©2023 Bostik, Inc. All Rights Reserved
All information contained herein is believed to be accurate as of the date of publication, is provided “as-is” and is subject to change without notice. To review our full U.S. Legal Disclaimer, visit: https://bostik.com/us/en_US/privacy-policy/legal-disclaimer