Jul 7, 2025 - 3-5 minutes
Address EV Battery Trends With Thermal Management Adhesives
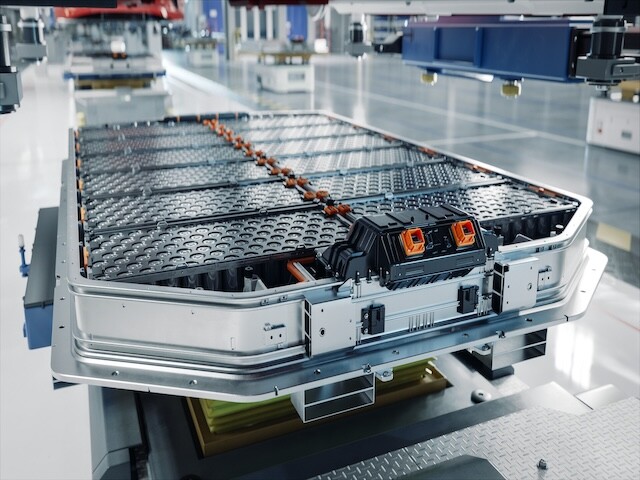
Learn about key trends impacting electric vehicle (EV) batteries and how thermal management adhesives help address those trends, boosting energy density, enhancing recyclability and increasing battery range.
When manufacturing electric vehicle (EV) batteries, you're likely aiming to increase the battery’s energy density, sustainability and range to optimize battery effectiveness.
However, achieving these goals simultaneously can be difficult, as there can be complexities in trying to create compact and optimized systems with effective thermal management. This is where thermal management adhesives can help.
Learn about important industry trends and which thermal management adhesives can be the right choice for your EV battery needs to address them.
Trend #1: Increasing Energy Density
One key trend impacting the EV battery manufacturing market is the demand to improve battery power storage capacity while reducing the battery size; in other words, increasing its energy density. This can help automakers deliver longer driving ranges, helping consumers go farther on a single charge while still maintaining interior space, performance, and efficiency.
This trend applies across the EV market, from compact cars to large SUVs; however, large vehicles require more power than small vehicles, which means they need more battery cells. Yet making the battery pack larger isn’t always feasible due to space constraints, weight distribution and vehicle design limitations. As a result, you may need to eliminate traditional cell holders and place cells closer together – which can lead to an entirely new battery design to increase energy density for large vehicles.
These new battery design requirements (compact and high-density) can create thermal management complications that not all adhesives can overcome. With cells packed more closely together, heat buildup becomes a greater risk.
How Thermal Management Adhesives Can Help:
In redesigning battery packs to fit more cells into tighter spaces, thermal management adhesives, such as thermally conductive adhesives (TCAs), help enable increased energy density by replacing traditional mechanical fasteners or cell holders that would take up space and reducing gaps between cells. Further, TCAs used in EV battery packs provide both structural bonding and thermal control. Formulated with thermally conductive fillers, such as ceramic particles or metal oxides, TCAs create efficient pathways for heat dissipation through the adhesive layer. The base polymer is formulated to maintain strong adhesion and flexibility, accommodating the thermal expansion and contraction of battery components. This balance of thermal conductivity, electrical insulation and mechanical strength helps TCAs meet EV battery design requirements for large vehicles where increased energy density is critical.
In particular:
- Two-component, epoxy (EP) TCAs are non-silicone solutions known for their high-strength bonding and customizable properties tailored to specific battery design needs. With thermal conductivity up to 3W/m.K*, they offer a range of viscosities suitable for fast joining and automated processes along with excellent chemical resistance to support long-term battery durability.
- Two-component, polyurethane (PUR) TCAs are also non-silicone solutions valued for providing thermal conductivity up to 1.5 W/m.K or higher* as well as high elongation, which provides elasticity to handle thermal cycling. These adhesives bond to substrates such as nylon, PET, PI, aluminum and steel; they maintain electrical insulation to help reduce the risk of electrical faults.
Additionally, you may also want to consider customized TCA formulations that meet the specific thermal and mechanical requirements of your battery design to help ensure high performance and long battery life.
Trend #2: Increasing Battery Removability and Recyclability
As EV batteries evolve, you may be increasingly focused on reducing environmental impact for any battery repair needs and end of life. This includes making it easy to take battery components apart as well as reuse and recycle valuable metal materials, such as aluminum, that can be costly and intensive to produce. By finding ways to increase battery removability and recyclability, you can help increase the circular yield for future products.
However, EV battery adhesives can be a barrier to reducing environmental impact if they lack debonding capabilities. For example, many traditional, silicone-based gap fillers offer high strength, but can pose battery component disassembly challenges. This is because they can either leave behind a hard-to-degrade residue or fully render the component unable to be separated down to its sub-parts. As a result, the battery component can’t be removed; it is discarded and fully replaced, contributing to landfill waste generation in addition to increased material usage. Without the ability to separate battery components, it can become difficult or impossible to recover and reuse valuable metals, leading to increased costs and environmental impact.
How Thermal Management Adhesives Can Help:
Certain thermal management adhesives, such as alternative, silicone-free gap fillers, are designed for removability to address repair needs and end-of-life disassembly as well as provide thermal conductivity and density to help prevent hot spots.
Available in one and two-component options, they help contribute to less waste production compared to other gap fillers:
- One-component, non-reactive gap fillers are non-curing, silicone-free materials that remain pliable over time. With a low oil separation (~0.3%), they maintain the same liquid viscosity throughout their lifespan, helping to ensure long-term stability with easy removability at the battery’s end of life.
- Two-component silyl-modified polymer (SMP) gap fillers are designed for automated, high-volume production. These gap fillers maintain a low bond strength with controlled viscosity and low compression forces. This aids in removal, allowing you to disassemble the battery module down to its sub-parts and reuse them if needed to reduce overall waste generation. Additionally, these SMP gap fillers are VOC-free to further enhance sustainability in the EV battery and remove hazardous materials.
Trend #3: Increasing Battery Range
Lithium-ion (Li-ion) cells, which are a type of rechargeable battery commonly used for their high energy density and light weight, can degrade faster when exposed to high temperatures, resulting in a shorter lifespan. New technologies like sodium-ion are starting to emerge to overcome those limitations.
While adhesives are not within the cell itself, there is still the concern of assuring everything works together effectively, especially when introducing new technologies such as sodium-ion. For example, if sodium-ion allows the battery to be optimized for a longer lifespan than lithium-ion inside the battery cell, the adhesives on the outside of those cells also must be formulated to provide strength and thermal management to maintain the same lifespan.
How Thermal Management Adhesives Can Help:
As previously mentioned, both TCAs and gap fillers help transfer heat away from a battery cell, helping to minimize imperfections and enhance efficient thermal performance outside the battery cell. This allows for more ease in switching to sodium-ion inside the cell, as you have the assurance the components outside the cells will be able to keep up with the extensive battery life compared to what was necessary for lithium-ion.
Thermally Conductive Adhesives (TCAs), as mentioned above, are formulated to be non-reactive with metals, ceramics, and plastics, helping to prevent corrosion or material breakdown. In particular, they provide:
- Thermal Stability: TCAs are built to perform across a wide temperature range, from -40°F to 302°F (-40°C to 150°C), helping to ensure reliable performance during charging, discharging and everyday driving conditions.
- Long-Term Durability: TCAs resist degradation from chemicals and humidity, helping to reduce the need for repairs or replacements.
- Flexibility: If desired, some TCAs can retain flexibility after curing, which allows them to absorb stress caused by thermal expansion and contraction. This flexibility helps prevent mechanical failures.
Gap Fillers, as previously mentioned, play a crucial role in optimizing thermal performance by eliminating air pockets that can impact heat transfer. Their ability to conform to surfaces and fill voids enhances battery efficiency and longevity:
- Hot Spot Mitigation: By filling the space between battery cells and heat sinks, gap fillers can prevent the formation of hot spots that can lead to overheating or damage. This helps with consistent thermal flow and protects sensitive components.
- Surface Conformability: Liquid gap fillers adapt to microscopic surface irregularities, creating a more uniform thermal interface. This improves heat dissipation and overall system performance.
Why Choose Bostik
As the adhesives solution segment of Arkema, Bostik offers a range of high-performing EV battery solutions to address both bonding and thermal management:
Thermally conductive adhesives (TCAs): We offer two-part, polyurethane or epoxy-based TCAs with strong mechanical adhesion and thermal conductivity. The formulations are customizable to achieve your specific viscosity, strength, flexibility or open time needs.
Thermally conductive gap fillers: Bostik has acquired Polytec PT, a company known for offering alternative thermally conductive gap fillers. With one- and two-component gap fillers that are silicone-free, these solutions help prevent air pockets to further enhance the heat transfer. Additionally, they are removable and repositionable to reduce material waste.
Along with thermal management, Bostik provides solutions for parts of the EV battery, helping you to rely on a one-stop-shop supplier for your adhesive requirements. Our team of experts works directly with you so that our solutions can meet your specific performance and processing requirements.
Are you interested in addressing key industry trends to enhance your EV battery manufacturing? Contact a Bostik expert to learn how we can help you improve thermal management to help optimize your EV battery applications.
*based on Bostik internal testing
Other Relevant Content:
How Alternative Thermally Conductive Gap Fillers Improve EV Battery Sustainability
Why EV Batteries Need Silicone-Free Thermally Conductive Gap Filler
©2025 Bostik, Inc. All Rights Reserved
All information contained herein is believed to be accurate as of the date of publication, is provided “as-is” and is subject to change without notice. To review our full U.S. Legal Disclaimer, visit: https://bostik.com/us/en_US/legal-disclaimer