Feb 28, 2025 - 3-5 minutes
Meet Your Goals with the Right Low Pressure Molding (LPM) Method
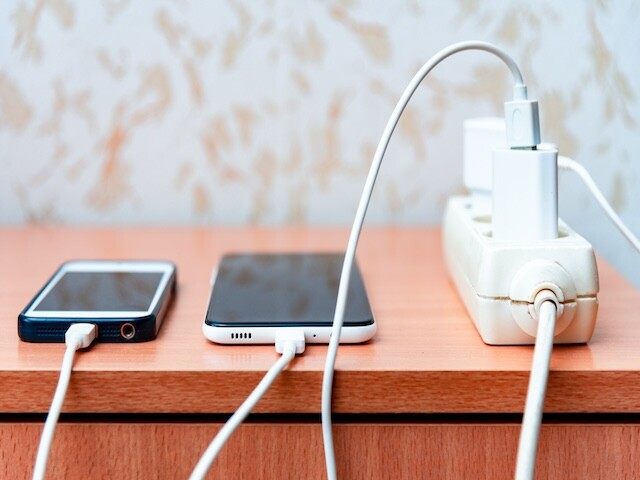
Learn how low pressure molding (LPM) can streamline your electronics encapsulation process, improve product quality, and enhance sustainability. Find out about the benefits of LPM over traditional potting methods and find the right adhesives and equipment for your needs.
As the electronics market continues to evolve, offering more complex products comprised of increasingly delicate parts, it’s a good idea to assess your encapsulation processes for circuit boards and cable assembly to ensure they are best suited to keep up with key needs.
In particular, if you are currently using the traditional potting process, you may want to consider how this method could be holding you back in the following ways:
Increased production time:
The traditional potting process requires you to mix a two-part, liquid system and then dispense it into a housing device. In addition to creating more production steps, it increases error likelihood. Further, the mixture then has to cure in an oven or on a shelf for 24 hours, which makes it difficult to maintain efficient production lines.
Decreased quality control:
When mixing the two-part, liquid system, it can be challenging to ensure the mixture ratio is exactly the same every time. The liquid may also spill and be difficult to control, which can impact the overall quality of your encapsulation and end-use product.
Reduced sustainability levels:
Because the potting process requires a specific housing component, you must invest in added material and parts, which increase both material and energy usage needs as well as the overall cost of encapsulating electronic devices.
Fortunately, an alternative method can overcome these challenges. Low pressure molding (LPM) is a cross between classic plastic injection and resin potting and is ideal for fragile components like connectors, onboard electronics, LEDs and printed circuit boards (PCBs). Find out how the right LPM method allows you to easily simplify production lines, improve product quality and increase sustainability.
How the Right LPM Method Helps You Meet Your Electronics Assembly Goals
Simplify Production Lines
Compared to the traditional potting process, the right LPM method reduces production time and complexity. As a one-part pellet system that cures within moments, you no longer need to combine two liquid solutions and wait for the mixture to cure. Instead, the process can be done in seconds. Additionally, because it is comprised of thermelt materials, you don’t need to then use a separate housing component; the materials become the encapsulation device, and the entire process is conducted in three simple steps:
- Add the circuit board into the mold.
- Inject the adhesive.
- Remove the encapsulated board from the mold
Improve Product Quality
As consumer desires for durable, quality electronic devices rise, it’s important for the encapsulation process to meet these standards each and every time. Unlike the traditional potting process, the right LPM method, which is based on pellets, makes it easy to achieve consistent, ideal product quality. It also offers:
- Increased resistance: The right LPM method incorporates adhesives that are resistant to moisture, high temperatures, harsh environments and solvents, which increases the longevity of electrical components.
- Improved aesthetics: The right LPM method also enables increased design options. With a lightweight, visually-pleasing design, brands and consumers will be satisfied with the look and feel of the encapsulated components.
Increase Sustainability
With an increasing global emphasis on reducing environmental impact, it’s a good idea to ensure your processes and products are able to meet this need. When compared to the traditional potting process, the right LPM method can help you improve your overall sustainability in the following ways:
- Reduce material usage: Because the right LPM method doesn’t require an additional housing component to encapsulate the electronics, you’re able to reduce material usage, saving costs and resources.
- Improve product end of life: When used with solvent-free, bio-based LPM adhesives, you are able to reduce the use of harsh chemicals in your production process. This can increase recyclability and end-of-life product sustainability.
How the Right Adhesive Can Help You Implement the Right LPM Method
In order to implement the right LPM method, it’s important to choose the right adhesive with it. This depends on a few different factors. Before selecting your solution, consider the following items:
Color options:
Some brands may prefer their encapsulations to be specific colors, while others may want transparent options. Ensure your adhesive choice comes in the colors you need.
Temperature stability:
Some electronic applications, such as circuit boards in automotive applications, may be exposed to high temperatures. Therefore, the LPM adhesive should offer high temperature stability, so it will not melt or degrade in these settings.
Resistance to harsh environments:
Some LPM adhesives are suitable for general purpose applications, while others offer high resistance to chemicals and flames. If your end-use applications are especially demanding, consider an adhesive equipped to handle these conditions.
Adhesive technology:
Hot melt polyamides offer easy processability and high resistance to harsh environments. Therefore, they are a good option to consider and are sustainable for many LPM applications. Available in mostly black or neutral colors, hot melt polyamides offer temperature resistance up to 150°C.
How the Right Adhesive Can Help You Implement the Right LPM Method
In order to implement the right LPM method, it’s important to choose the right adhesive with it. This depends on a few different factors. Before selecting your solution, consider the following items:
Color options:
Some brands may prefer their encapsulations to be specific colors, while others may want transparent options. Ensure your adhesive choice comes in the colors you need.
Temperature stability:
Some electronic applications, such as circuit boards in automotive applications, may be exposed to high temperatures. Therefore, the LPM adhesive should offer high temperature stability, so it will not melt or degrade in these settings.
Resistance to harsh environments:
Some LPM adhesives are suitable for general purpose applications, while others offer high resistance to chemicals and flames. If your end-use applications are especially demanding, consider an adhesive equipped to handle these conditions.
Adhesive technology:
Hot melt polyamides offer easy processability and high resistance to harsh environments. Therefore, they are a good option to consider and are sustainable for many LPM applications. Available in mostly black or neutral colors, hot melt polyamides offer temperature resistance up to 150°C.
How the Right Equipment Can Help You Implement the Right LPM Method
The right LPM method also entails using the right equipment, which can depend on several factors. As you determine your ideal equipment, consider the following:
Molding area size:
Some injection equipment is better suited for small circuit boards, while other solutions cater to larger ones. Make sure the equipment you choose can accommodate your parts.
Adhesive performance:
If your application requires superior adhesion, this can impact the type of equipment you choose. Select an equipment option that is compatible with adhesives that provide quick wet out, optimal adhesion and short run times to keep production speeds fast while maintaining quality bonds.
Output needs:
For high volume production, automated systems may help you keep lines moving as quickly as possible. Conversely, low volume production and prototype testing needs may be more compatible with handheld equipment.
LPM injection equipment also can come in a few different formats. There are several advantages to each option:
Horizontal injection equipment:
Ideal for larger parts, this equipment can process high-viscosity materials with an attached melt tank.
Vertical injection equipment:
These options provide superior wet out and adhesion while maintaining fast cycle times due to a short runner.
Semi-automatic and handheld equipment:
For higher outputs, semi-automatic equipment can keep lines moving quickly. More delicate work can be accomplished with handheld options.
How Bostik and LPMS Can Help You Implement the Right LPM Method
We understand the importance in finding the right adhesive and equipment to ensure your electronic components can be encapsulated quickly and easily while possessing great performance. Therefore, Bostik and Low Pressure Molding Systems USA (LPMS), a leading provider of LPM equipment, tooling services, materials and contract manufacturing, have partnered together to offer you the right LPM method that makes accomplishing your goals easy.
This partnership enables you to:
- Encapsulate parts safely in seconds and increase production throughput
- Simplify the protection process by reducing the number of manufacturing steps
- Enhance processing flexibility to easily protect even your most sensitive electronics for the most demanding applications
“This partnership has helped our customers avoid frustrating delays for raw materials due to Bostik’s vertical integration with Arkema. Not only that, but when Bostik and LPMS experts help you find the right adhesive and equipment combination for your application, you will experience shortened cycle times, improved product quality and increased cost efficiencies.” - Brian Betti, President of LPMS USA
If you’d like to learn more about how the LPM process can help you achieve your goals, contact a Bostik expert today, or visit LPMS USA.
Other Relevant Content:
Low Pressure Molding Adhesives
Why Polyamide Adhesives in Low Pressure Molding Are Revolutionizing Electronics Overcome Manufacturing Challenges with Low Pressure Molding Adhesives