May 8, 2023 - 3-5 minutes
Why Choose UV Over Hot Melts and Solvents for Tape, Graphic Applications
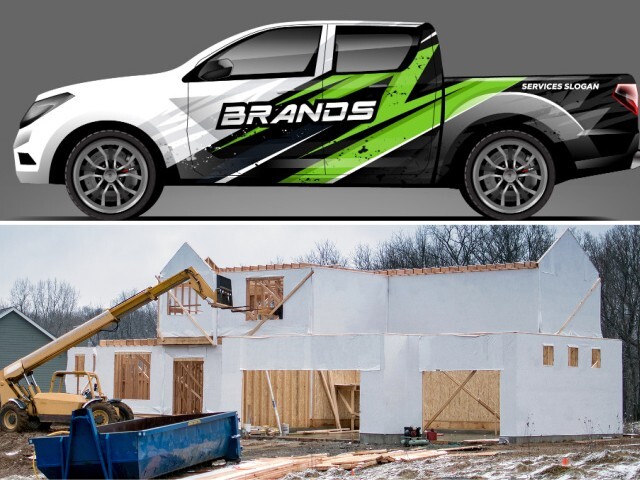
Learn how UV pressure sensitive adhesives can help overcome challenges in coating tapes and graphics.
Like many converters, you may be using solvent acrylic or hot melt pressure sensitive adhesives (PSAs) to coat tapes and graphics. However, both of these adhesive technologies pose certain limitations, whether due to environmental concerns or insufficient performance capabilities. Ultimately, these limitations can make it challenging for you to meet customer needs and expand your revenue opportunities.
However, by switching to UV PSAs, you’re able to easily overcome these limitations.
However, by switching to UV PSAs, you’re able to easily overcome these limitations.
What are UV PSAs?
UV PSAs are a 100% solids, pressure sensitive adhesive technology. Based on acrylic chemistry, they contain zero solvents and work well in the following applications:
- Graphics: vinyl films for vehicle wraps and transit advertising
- Building and Construction: seaming, flashing, mounting and house wrap tapes
How UV PSAs Overcome Limitations with Solvent PSAs
When coating solvent PSAs, you must take the following into account:
1. Solvent PSAs are not 100% solids. This means that you need to purchase more adhesive in order to obtain the amount of adhesive needed for your application, as a percentage of the adhesive is a solvent that gets burned off.
2. Solvent PSAs are considered hazardous materials. Because solvent PSAs are flammable, they pose safety concerns. They need to be stored inside and according to EPA regulations, which can make storage costly and complex. Additionally, when manufacturing with solvent PSAs, you need certain equipment and ventilation systems in place to account for the VOCs; both of these can add complexity as well as equipment maintenance costs. Further, when transporting solvent PSAs, you are likely to be subjected to higher shipping costs than with non-hazardous materials.
3. Solvent PSAs require a large footprint. Additionally, because solvent PSAs require drying ovens, it can be challenging to fit many production lines in a small plant space. This, in addition to the hazardous material regulations, may limit the number of lines you can have at your plant, which ultimately can impact your ability to meet customer output demands.
4. Solvent PSAs limit production speeds. Because you need to pause and allow time for the solvent to burn off, your production line efficiencies are limited. Additionally, if you need a thick coat weight, it may take several production passes before your application achieves the desired level, given that you need to account for the solvents. Further, because of the added equipment, associated maintenance, storage and transportation requirements, solvent PSAs make it challenging to produce products quickly.
5. Solvent PSAs are not environmentally sustainable. Because they are formulated with solvents and contain VOCs, these PSAs can pose harm to the environment and also contribute to:
a. Increased energy costs: Drying ovens need to constantly run during production time.
1. Solvent PSAs are not 100% solids. This means that you need to purchase more adhesive in order to obtain the amount of adhesive needed for your application, as a percentage of the adhesive is a solvent that gets burned off.
2. Solvent PSAs are considered hazardous materials. Because solvent PSAs are flammable, they pose safety concerns. They need to be stored inside and according to EPA regulations, which can make storage costly and complex. Additionally, when manufacturing with solvent PSAs, you need certain equipment and ventilation systems in place to account for the VOCs; both of these can add complexity as well as equipment maintenance costs. Further, when transporting solvent PSAs, you are likely to be subjected to higher shipping costs than with non-hazardous materials.
3. Solvent PSAs require a large footprint. Additionally, because solvent PSAs require drying ovens, it can be challenging to fit many production lines in a small plant space. This, in addition to the hazardous material regulations, may limit the number of lines you can have at your plant, which ultimately can impact your ability to meet customer output demands.
4. Solvent PSAs limit production speeds. Because you need to pause and allow time for the solvent to burn off, your production line efficiencies are limited. Additionally, if you need a thick coat weight, it may take several production passes before your application achieves the desired level, given that you need to account for the solvents. Further, because of the added equipment, associated maintenance, storage and transportation requirements, solvent PSAs make it challenging to produce products quickly.
5. Solvent PSAs are not environmentally sustainable. Because they are formulated with solvents and contain VOCs, these PSAs can pose harm to the environment and also contribute to:
a. Increased energy costs: Drying ovens need to constantly run during production time.
However, UV PSAs offer the following advantages compared to solvent PSAs:
- Extended product mileage: UV PSAs are 100% solids. Unlike solvents, there is nothing within the product that needs to first burn off and essentially goes to waste. This means you can purchase less product than solvent PSAs while receiving the same amount of actual adhesive.
- Eliminated risk: They also do not contain any harmful materials and are a more stable product than solvent PSAs. This reduces storage, transporting and manufacturing concerns, complexities as well as costs.
- Reduced plant footprint: Further, manufacturing with UV PSAs does not require any drying ovens, unlike solvent PSAs, and production lines up less space as a result. This enables plant space to be more efficiently used in comparison.
- Increased production efficiencies: UV PSAs can run much faster than solvent PSAs; no downtime is needed for the solvent to burn off, allowing you to more efficiently meet customer output needs. Additionally, you’re able to achieve a much higher coat weight in a single pass, which further keeps production lines moving quickly.
- Improved environmental impact: In addition to being inherently better for the environment than solvents, UV PSAs also:
- Reduce energy costs: No drying ovens are needed.
How UV PSAs Overcome Limitations with Hot Melt PSAs
While hot melt PSAs are 100% solids like UV PSAs and do not have the same environmental concerns as solvent PSAs, they still pose limitations. For example:
Hot melt PSAs lack needed performance capabilities for demanding applications. In particular, they do not offer sufficient:
Due to hot melt PSAs’ limitations, you may be limiting yourself in the following ways:
Increased performance capabilities: UV PSAs offer performance levels on par with solvents but without the environmental concerns. For example, UV PSAs possess:
Hot melt PSAs lack needed performance capabilities for demanding applications. In particular, they do not offer sufficient:
- Long-term stability
- Shear levels
- Adhesion to certain substrates, such as metals, metals, glass, plastics, aluminum, polycarbonate, and vinyl
- Plasticizer, UV or chemical resistance
- Clarity for certain application needs
Due to hot melt PSAs’ limitations, you may be limiting yourself in the following ways:
- Your ability to offer customers expanded options
- Your potential revenue, as you’re unable to tap into a key market space of high-value applications
Increased performance capabilities: UV PSAs offer performance levels on par with solvents but without the environmental concerns. For example, UV PSAs possess:
- High durability and shear levels
- Broad adhesion capabilities
- Excellent plasticizer and chemical resistance
- High clarity
How to Switch to UV PSAs
If currently using solvent PSAs, you will need to invest in a UV PSA production line. However, like many converters, you may have been looking to expand your solvent PSA line anyhow to increase your revenue potential. Comparatively, installing a UV PSAs is more cost effective in the following ways and enables you to reduce costs overall due to their:
- Decreased energy usage
- Increased production efficiencies
- Reduced plant footprint
Why Choose Bostik as Your UV PSA Supplier?
Backwards Integration
As an Arkema company, Bostik offers a wholistic approach to serving customers, which is unmatched in the industry. Because we are backwards integrated, we are able to source our own polymers in house. This enables us to offer a better supply position compared to other suppliers. Additionally, we are able to develop custom UV initiators, which allows us to offer increased differentiation to our customers. This, in turn, enables them to have more differentiated products, too.
Custom Formulation
At Bostik, we also have the technical expertise and dedicated resources to adjust product formulas as needed to meet specific customer needs. This capability further helps our customers stand out in their own market space.
Ready to learn more about our UV PSAs? Contact a Bostik expert today!
Contact an expert
As an Arkema company, Bostik offers a wholistic approach to serving customers, which is unmatched in the industry. Because we are backwards integrated, we are able to source our own polymers in house. This enables us to offer a better supply position compared to other suppliers. Additionally, we are able to develop custom UV initiators, which allows us to offer increased differentiation to our customers. This, in turn, enables them to have more differentiated products, too.
Custom Formulation
At Bostik, we also have the technical expertise and dedicated resources to adjust product formulas as needed to meet specific customer needs. This capability further helps our customers stand out in their own market space.
Ready to learn more about our UV PSAs? Contact a Bostik expert today!
Contact an expert
©2023 Bostik, Inc. All Rights Reserved
All information contained herein is believed to be accurate as of the date of publication, is provided “as-is” and is subject to change without notice. To review our full U.S. Legal Disclaimer, visit: https://bostik.com/us/en_US/privacy-policy/legal-disclaimer
All information contained herein is believed to be accurate as of the date of publication, is provided “as-is” and is subject to change without notice. To review our full U.S. Legal Disclaimer, visit: https://bostik.com/us/en_US/privacy-policy/legal-disclaimer