Apr 24, 2025 - 3-5 minutes
Why You Should Consider a More Sustainable Alternative to Potting
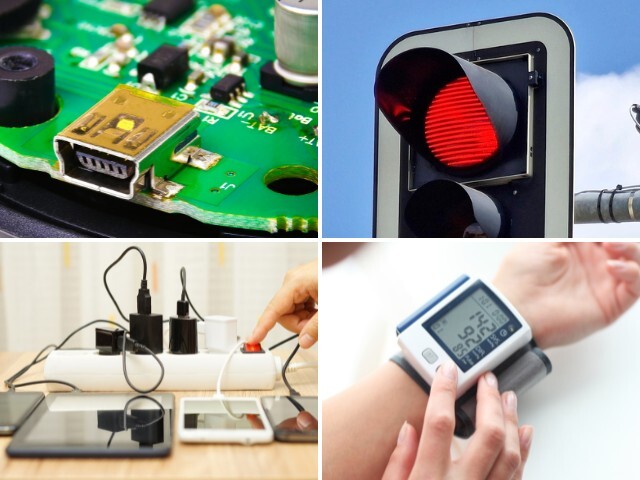
Learn how low pressure molding (LPM) offers a more sustainable alternative to traditional potting methods for encapsulating electronic components. Read about the limitations of potting technologies and how Bostik’s Thermelt® low pressure molding polyamides can help you achieve your sustainability goals.
When encapsulating electronics, you likely want to increase sustainability in both your finished products and manufacturing processes. To do so, you want to be aware how you are contributing to environmental impact – however, this can be challenging when using potting methods.
While potting is a common way to protect electronics, it poses key limitations to accomplishing sustainability goals due in large part to the solutions needed to conduct it. That’s why you should consider low pressure molding (LPM), a manufacturing process that uses more sustainable resins and entails injecting molten plastic material into a mold to gently encapsulate the devices.
Find out the limitations potting technologies pose, how LPM resins overcome them and how Bostik’s Thermelt® low pressure molding polyamides can help you further address sustainability goals.
How does potting as an encapsulation method itself pose sustainability limitations?
Potting requires at least seven production steps to complete the encapsulation process. Each step can be time-consuming and pose error likelihood, which can increase overall production time, energy usage and waste production and hinder overall sustainability.
How do potting technologies pose sustainability limitations?
Potting technologies are typically two-part polyurethanes and two-part epoxies. They inherently pose sustainability challenges due to:
Mixing requirements
Potting requires mixing to blend two components together, which increases error likelihood that may therefore require additional material replacements.
Extensive processing time
Curing for potting technologies can cause additional production downtime and energy usage:
- Two-part polyurethanes can cure within 24 hours at room temperature and be accelerated with heat; however, this increases energy usage and requires additional equipment
- Two-part epoxies can cure within 24 hours; however, temperature, humidity and the specific formulation itself can vary and therefore impact the processing time
Hazardous materials
Potting technologies can contain volatile organic compounds (VOCs) in their formulation such as isocyanates, which are a harmful substance that pose toxicity concerns and can contribute to carbon emissions. During the application and curing process, these substances can evaporate into the air, increasing risk of potential respiratory issues or sensory irritation for workers handling these materials.
Carbon emissions due to increased weight
Two-part polyurethane potting technologies tend to have high density that leads to an increase in the overall weight of the product, especially for large or complex assemblies where weight may already be a factor. While two-part epoxies may have slightly less density than two-part polyurethanes, they may require extra properties to be added to their formulation to yield capabilities like electroconductivity, which can increase the overall weight of the end-use product. Due to these technologies’ densities, they can increase fuel usage and carbon emissions during shipping if the products are heavier to transport.
Unlike potting, LPM only requires three steps of injecting the resin, molding and testing the finished electronic component. This reduction in production steps helps reduce both energy usage and error likelihood that may result in using additional materials for replacements. Additionally, LPM utilizes the technique of skylining; this method uses less resin than potting because it follows the contours of the electronic component rather than filling an entire closure. Therefore, this results in an end-use product with less weight to decrease overall carbon emissions during transport.
This image outlines how LPM processes are simplified compared to potting:
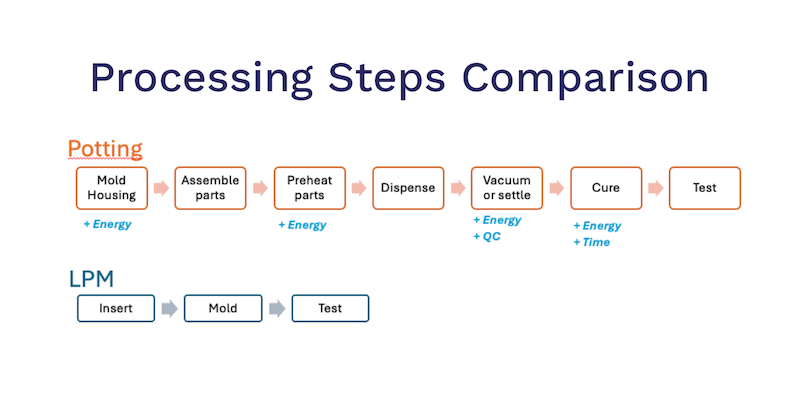
How do LPM resins overcome potting technologies’ sustainability limitations?
Unlike potting, which uses two-part technologies, LPM resins can be one-part hot melt polyamides (HMPAs), offering:
Enhanced formulation
HMPAs are comprised of 100% solids, which eliminates solvents or other hazardous substances from their formulation. This increased sustainability in the formulation helps LPM processes improve worker safety over potting methods.
Reduced carbon emissions
Additionally, HMPAs typically have less density than two-part polyurethanes and two-part epoxies. By using a lighter weight resin and reducing the volume of material used to protect the electronic component, LPM decreases the overall weight of the end-use product. This also helps improve overall fuel usage during shipping to decrease carbon emissions.
Simplified processing
Unlike two-part polyurethanes and two-part epoxies, HMPAs are one-component and do not require mixing for LPM. The thermoplastic properties in HMPAs also enable LPM to set rapidly for fast cycle times, helping to reduce overall energy usage during production.
What low pressure molding solution should I choose and why?
Bostik’s Thermelt® is supplied as a resin that gets melted and injected into a mold to encapsulate the electronic part, such as onboard electronics, LEDs and PCBs (printed circuit boards). Thermelt® also can be used to address electronic encapsulation in luxury goods, medical devices, automotive, air and oil filtration and footwear markets. Along with protecting and sealing delicate electronic components against moisture, dust, dirt and debris. Thermelt® offers numerous sustainable features:
Removal of hazardous materials
Thermelt® low pressure molding technologies are solventless solutions that are up to 90% bio-based*, made from raw materials including rapeseed oil that is produced into diacids. By eliminating solvents and incorporating bio-sourced materials, Thermelt® removes hazardous materials commonly found in potting technologies. Thermelt® also consists of less material than potting, helping reduce material while also manufacturing a lighter weight part.
Ease of processing
- Reduced energy usage: Simplified to a single, fast process, Thermelt® is a cross between classic plastic injection and resin potting. Unlike potting technologies, this one-component solution offers fast cycle times of 90 seconds and eliminates mixing steps, helping to speed up processes and decrease overall energy usage.
- Less material waste: Thermelt® offers a range of low viscosities to provide low process pressure for delicate electronic structures or sensitive materials. With a low temperature range of 356°F (180°C) to 446°F (230°C), Thermelt® helps minimize damage during manufacturing, especially for electronic components with heat-sensitive elements. It will also protect sensitive solder joints from melting and breaking the circuit. With various options for viscosities and temperature ranges, Thermelt® makes it easy to decrease material usage since there are less chances for errors that require material replacements to occur.
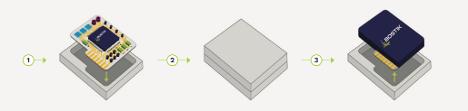
What are additional benefits to using Thermelt®?
The Thermelt® product range includes grades with:
- Environmental resistance: Thermelt® helps resist temperatures (-40C to 130C), chemicals, water and UV to enable a long-lasting electronic component.
- Sterilization resistance to meet ISO certification: Certain Thermelt products have completed ISO certifications, rendering them confidently suitable for use in medical devices, including wearables, continuous glucose monitors and smart health patches as well as surgical tools. In addition to offering the same performance capabilities they’re known for, these products have been tested to ensure they do not cause sensitization or irritation if in contact with skin.
- Low Tg and high adhesion: The Thermelt® product range makes it easy to choose a solution that provides your desired performance strength and molding capabilities for demanding substrates or delicate applications.
- UL 94 V-0 rating: This rating means the product self-extinguishes within 10 seconds when exposed to a flame and won’t drip flaming particles for increased end-user safety.
Why should I work with Bostik and use Thermelt®?
As the adhesives solutions segment of Arkema, Bostik’s team of experts can provide the knowledge you need to implement Thermelt® into your production. We are here to provide:
- Technical support: From trial testing to troubleshooting assistance, our team members consist of LPM experts and specialists who can offer in-person support with your assembly. We work with you to test your materials with our product range, helping to ensure you find the best solution for your performance needs. Further, we’ll assist with getting the solution to operate efficiently on your production lines. We also offer support with product training and using automated dispensing equipment properly.
- Reliable partnerships: We are here to develop partnerships with equipment producers that help ensure your machinery operates efficiently with a high-performance solution like Thermelt®.
- Global sourcing: As mentioned above, through our parent company Arkema, we are vertically integrated to provide Thermelt® low pressure molding technologies wherever you are located.
Are you ready to use a low pressure molding technology that can provide a more sustainable electronic assembly while providing high performance and simplified processes? Contact a Bostik expert to learn which solution in our Thermelt® product range may be right for you.
*The biobased content is the % breakdown based on a carbon (EN16640 or ASTM D6866) or a mass (EN16785-2) ratio.
Other Relevant Content:
Low Pressure Molding Adhesives
Overcome Manufacturing Challenges with Low Pressure Molding Adhesives
Meet Your Goals with the Right Low Pressure Molding (LPM) Method
Why Polyamide Adhesives in Low Pressure Molding Are Revolutionizing Electronics Protection
Thermelt® is a registered trademark of a company of the Arkema Group
©2025 Bostik, Inc. All Rights Reserved
All information contained herein is believed to be accurate as of the date of publication, is provided “as-is” and is subject to change without notice. To review our full U.S. Legal Disclaimer, visit: https://bostik.com/us/en_US/privacy-policy/legal-disclaimer