May 30, 2023 - 3-5 minutes
Address Key Challenges to Achieve Label Circularity
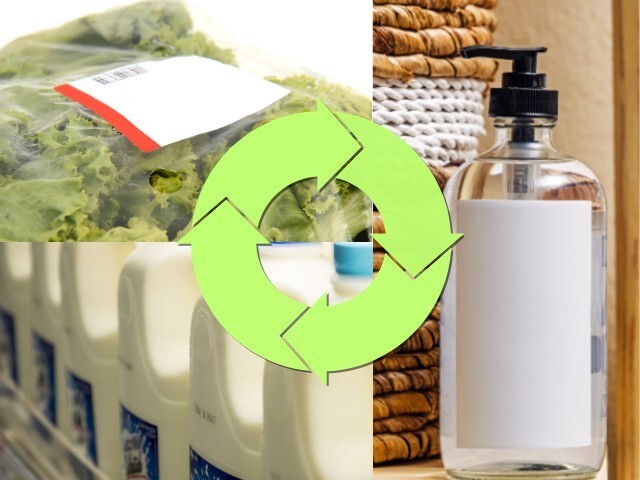
Learn about the challenges label converters face in achieving circularity and how the right label adhesive can make it easy to accomplish for PET packaging labels.
What is Circularity?
Challenges Achieving Circularity with Labels
- Recycling stream contamination: If a PET package still has part of the label particles on it after the initial recycling stream, it will be unable to form into new packaging through circular mechanical recycling. This is because the label particles have not fully washed off. In order to contribute to the circularity of an overall package, the end-use label must have proper wash-off capabilities to avoid contaminating the overall recycling stream, which can be difficult to achieve. PET applications such as bottles and trays also can be taken out of the recycling stream if they have haziness or yellowing as a second-generation plastic material.
- Material waste: The label’s liner will be disposed after the label itself is adhered to a substrate, resulting in significant production waste for the end-user. For label manufacturers, applying the liner to the label is a significant step that contributes to a plant’s overall energy usage.
- Energy usage: Labels that are manufactured from fossil-based raw materials, such as oil or gas, require more energy usage to produce. In order to reduce the overall energy usage, manufacturers must find ways to reduce fossil-based raw materials in their processes to improve a plant’s carbon footprint.
How Adhesives Address Labels’ Circularity Challenges
Adhesives are a key component to the end-use label and can help labels achieve circularity in the following ways:
Wash-off capabilities within the adhesive formulation will allow the label to cleanly separate from the substrate during the repulp process. This will prevent any residue from the adhesive or label layers from contaminating the recycle stream, allowing a PET application to be used to form new products.
Linerless label adhesives eliminate the need for a release liner, which decreases waste production along with a facility’s overall energy usage.
Bio-based adhesives can help reduce energy usage and improve a plant’s carbon footprint. Bio-based raw materials are partially or wholly derived from biomass, which yield less carbon emissions compared to traditional, fossil-based raw materials that are based on gas oils. Further, if bio-based adhesives are used within linerless labels, you can reduce your transportation carbon emissions even more because you can fit more labels into a single shipment.
Challenges Achieving Circularity with Certain Label Adhesives
- Ensuring the label adhesive meets recycling standards: As a converter, you can work with the Association of Plastic Recyclers to see if your label adhesive meets key guidelines to provide wash-off capabilities, but this typically takes a minimum of six months to test. It is also not guaranteed the label adhesive will meet APR approval; if it doesn’t, you will have to decide whether to start the process over again, which can take up time and resources, potentially straining production.
- Complexities producing linerless labels: You may be concerned about investing in linerless label adhesives, because you may not fully understand how to gain the most production efficiencies from this option. With upfront costs to purchase linerless equipment, this may be viewed as a deterrent that could require additional training or downtime to get fully adjusted. As a result, you may worry this adjustment period could use up additional plant energy, adding to your overall carbon footprint.
- Questioning the bond strength: While fossil-based, hot melt adhesives are known for providing high tack levels that can adhere to difficult substrates, you may be unsure whether a sustainable option, such as bio-based, hot melt adhesives, can do the same. Further, since bio-based adhesives are relatively new for the industry, it may be difficult to find enough information to feel confident about going bio-based.
How the Right Adhesives Overcome Adhesive Challenges with Achieving Label Circularity
The right label adhesive will help you easily implement your end-use label into the overall circular system for packaging applications, while still getting the necessary performance and production efficiencies to address key challenges.
Meeting recycling requirements
By choosing a wash-off label adhesive that’s already proven to meet or exceed critical guidance criteria for PET recycling, you’ll eliminate a significant amount of work ensuring your end-use label contributes to the circular system. Then you can instead focus on the label layers that still need to meet this approval, saving valuable production time, resources and testing costs.
Improving plant efficiencies
Investing in linerless label adhesives will help you reduce both costs and plant energy usage over time. Without a liner, the design structure of a linerless label places the labels closer together, decreasing the variable print length and fitting twice as many labels per roll compared to traditional labels. This helps reduce overall production time by getting more labels produced with fewer materials, also decreasing energy usage. Linerless label adhesives can also be applied with a reduced coating weight, allowing you to save costs by getting more labels produced per adhesive drum.
Maintaining performance strength
Just like fossil-based, hot melt adhesives, you can rely on bio-based, hot melt adhesives to have adjustable tack levels for similar bond strength to substrates such as paper, corrugate, glass and stainless-steel. Bio-based adhesives also offer strong bonding to facestocks with polypropylene (PP), polyethylene (PE) and high-density polyethylene (HDPE). This allows bio-based adhesives to still be reliable for applications that require minimal shear such as ecommerce, food, beverage, weigh scale, health and cosmetics.
How Bostik’s Label Adhesives Increase Circularity
Our all-temperature, wash-off label adhesive addresses an unmet need for cold temperature applications that also increases PET packaging circularity. Our solution is proven to meet or exceed critical guidance criteria by the Association of Plastic Recyclers, enabling converters to increase overall recycling for both end-use labels and PET packaging. It does not require surface treatment, simplifying production steps and improving energy usage. This wash-off label adhesive remains tacky with a good initial bond down to 0°F (-17°C), allowing you to rely on one wash-off label adhesive for all temperature requirements.
Our linerless label adhesives are designed to decrease material waste and overall energy usage. Compatible with UV silicone release coatings, our linerless label adhesives are based on hot melt pressure sensitive adhesives and provide lower coat weights with the same performance standards as linered labels. Further, linerless labels can be used in direct thermal printers and offer high tack and shear resistance to avoid jamming. By cutting the label’s overall material in half, the converter will save downtime and overall costs on production waste, helping improve energy efficiencies.
Our bio-based, hot melt adhesives are available in various percentages of bio-based molecules that are certified by the testing method ASTM D6866-22. By forming a bond upon heat activation and cooling at room temperature, these bio-based, hot melt adhesives provide the same bond strength at low coat weights like fossil-based, hot melt adhesives, allowing for a streamlined production with minimal changeouts.
Additionally, our Bostik team will provide the technical support to assist in trial testing and custom formulations, ensuring our label adhesives provide the performance and processing capabilities necessary.
Want to find ways to improve circularity with end-use labels? Contact a Bostik expert to learn how the right label adhesive can help labels enhance the circular system in packaging.
Contact an Expert
All information contained herein is believed to be accurate as of the date of publication, is provided “as-is” and is subject to change without notice. To review our full U.S. Legal Disclaimer, visit: https://bostik.com/us/en_US/privacy-policy/legal-disclaimer