Oct 20, 2023 - 3-5 minutes
3 Reasons You Need the Right Extrudable Reseal Supplier
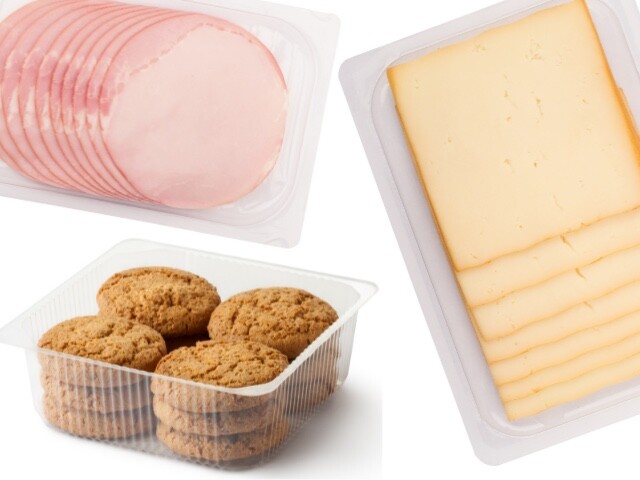
Discover the advantages of extrudable hot melt reseal technology for reseal packaging, and learn how choosing the right supplier can ensure reliable sourcing, efficient processing, and enhanced sustainability, while avoiding common challenges in the industry.
For reseal food packaging applications such as meat, cheese and confectionary, you likely know that reseal packaging is known for providing:
- Increased package usage: By offering a minimum of ten reseals*, reseal packaging allows the end user to reuse the original packaging until the food is gone without requiring a secondary storage container.
- Reduced material and food waste: Reseal technology can be used in multi-layer film to replace rigid lid or clamshells, reducing plastic material by 30%* and prolonging the package lifespan while keeping food fresh.
- Enhanced recycling capabilities: Reseal packaging can improve the end user’s environmental footprint when the resealable lidding film is used with APET trays because it amplifies the package’s overall recyclability.
However, achieving these elements is contingent upon choosing the right reseal adhesive technology from a supplier that has your needed reseal technology, such as extrudable hot melt, readily available and that the product can meet the desired processing criteria and performance levels. Learn more about the challenges that can occur if these items are not met and how right supplier for extrudable hot melt reseal technology can make it easy to be successful.
#1: Supply Sourcing Issues
After taking the steps to establish a supplier, it’s important to ensure the product is delivered on time when and where you need it. Further, it’s highly recommended to determine whether your supplier considers their extrudable hot melt reseal technology as a key segment product, ensuring they will not drop it from their product portfolio in the near future.
Managing both of these issues can take valuable time away from other production needs, becoming a costly setback. Additionally, it can cause you to lose trust with your current supplier and require you to invest more time into sourcing a new supplier.
#2: Limited Processing Options
It’s also important to understand the right supplier may not be able to offer extrudable reseal and assist with implementing it into your existing equipment. This could increase complexities and downtime if you must address troubleshooting issues yourself, resulting in delayed end-use products for brand owners. If you have to manage problems without expertise from your supplier, you may miss opportunities to reduce material waste that the supplier could have advised about. This may cause you to end up with more material scraps or a lower throughput rate if you are not using an efficient process to extrude adhesive, which may also decrease your plant’s manufacturing efficiencies.
#3: Insufficient Performance Levels
Further, you want to ensure your supplier’s extrudable hot melt reseal technology meets desired end-use performance levels, such as the package’s overall lifespan and tray recyclability. If the supplier’s product cannot provide this, it could impact other parts of the value chain; for instance, it may prevent brand owners from meeting consumer interests or addressing concerns from non-governmental organizations (NGO). Likewise, if a supplier cannot customize formulations to fit your specific needs, the end-use package may not offer as many reseals as it potentially could if the formulation was tailored to your requirements.
Along with providing sustainable benefits, it’s important to clarify whether the supplier’s product still passes industry standards such as FDA compliance. Further, your supplier should be able to show you whether the extrudable hot melt reseal technology is compatible with your desired substrates and offer recommendations based on the performance results. If a supplier cannot provide this insight, it may cost you additional time and expenses testing to ensure your end-use application complies or performs with your substrates.
Advantages of Working with the Right Reseal Supplier
Reliable Supply Sourcing
To help avoid supply sourcing issues, the right supplier offers:
-
Wide reseal technology portfolio: A supplier that offers a wide array of reseal products, even beyond extrudable hot melt reseal, helps ensure supply continuity as you will have multiple reseal options.
-
Competitive product advantages: By providing reseal solutions that offer similar performance advantages, as well as additional features such as anti-blushing, you can ensure your supplier is prioritizing their reseal product line as a key product segment and continue working to develop new innovative products to meet the ever-changing market needs.
Along with a full portfolio, the right supplier will provide experts to help ensure their products work effectively with equipment already in use. This can help save valuable time and resources to conduct testing and find the right solution. It can also make it easier to address any production problems that may arise, reducing overall maintenance downtime.
Efficient Processing Capabilities
The right supplier will offer extrudable reseal products and assist in implementing them into your existing equipment to ensure processing efficiencies are high. In particular, consider a supplier that offers:
-
Versatile use: These solutions should be capable of processing on conventional, multi-layer cast and blown film lines and be designed to coextrude well next to a various polymers. This will allow usage of the same extrudable hot melt reseal technology across multiple film structures for both food and non-food applications.
-
Enhanced functionality: The right supplier’s extrudable hot melt reseal technology can be functional without laser scoring. This is beneficial, because it allows for resealable films to be sealed at the same rate as traditional, single-peel films, which improves end-use functionality at the processing rate. Furthermore, certain extrudable hot melt grades have longer shelf life, up to nine months, to ensure optimal processing windows.
-
Customization: As mentioned before, by providing a portfolio with various adhesive formulations, you can find the right solution quickly. However, to further keep efficiencies high, consider a supplier that is able to customize the formulation if necessary to account for unique applications or processing capabilities.
Performance Levels
The right supplier will work to ensure products offer needed performance levels, such as:
-
Enhanced sustainability: A supplier that develops reseal products to enhance overall sustainability, such as prolonging plastic packaging lifespan, can make it easier for you to accomplish your goals. Additionally, by choosing a supplier that designs products for APET mono-material trays, your tray can be recyclable as well. Further, consider how a supplier can provide measurable achievements of how their products reduce environmental footprint to meet sustainability initiatives.
-
Compliance: A supplier that accounts for industry standards will have the knowledge to help test whether their extrudable hot melt reseal technology is compatible with the desired substrates and if it meets FDA compliance. This can help save valuable resources and streamline the scale-up process.
Why Bostik is the Right Supplier for Extrudable Hot Melt Reseal Technology
In addition to meeting the needs above, Bostik was the first to patent m-resins, the market’s first extrudable hot melt reseal technology. We offer a portfolio of both flange seal tray and die-cut, coater-ready reseal packaging options. Further, we provide:
-
Global sourcing: As the adhesives division of Arkema, we are vertically integrated to provide solutions around the world, helping streamline supply chain concerns to deliver end-use products in a timely manner.
-
Technical support: From on-site testing to troubleshooting, our team is here to help find the right coater-ready solution that will enhance production efficiencies. We are also continually developing new formulations to help address unmet needs and have pilot capabilities to provide proof-of-concept options before going into production.
-
Sustainable certifications: Our m-resin reseal technology meets the Recyclass recyclability certification for PE film and is proven not to contaminate the tray. This was also determined via certification by Ecosense Foundation for PE trays. Our m-resins allow a package to use reseal lidding and for the tray to still be recycled via mechanical recycling.
Ready to begin using our extrudable hot melt reseal technology? Contact a Bostik expert to learn how to get started as soon as today!
*based on internal testing
Other Relevant Content:
How Resealable Packaging with M-Resins Reduces Plastic and Food Waste
VIDEO: Why You Need to Know About M-Resins for Resealable Packaging Applications
©2023 Bostik, Inc. All Rights Reserved
All information contained herein is believed to be accurate as of the date of publication, is provided “as-is” and is subject to change without notice. To review our full U.S. Legal Disclaimer, visit: https://bostik.com/us/en_US/privacy-policy/legal-disclaimer