Jun 1, 2023 - 3-5 minutes
Get More Out of Your Reseal Packaging Technology
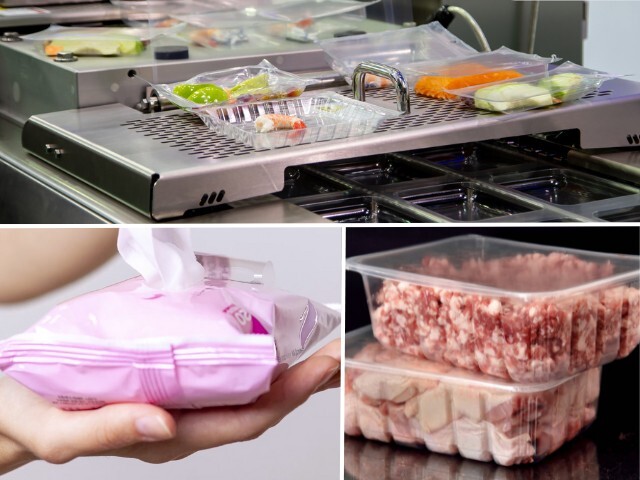
Discover how choosing the right reseal adhesive technology can overcome common challenges in packaging while unlocking additional capabilities. Learn how to mitigate blushing, work with different packaging structures, and enhance your brand's sustainability efforts.
As a converter, you know reseal packaging technology can help:
- Decrease single-use packaging: Reseal packaging technology provides a minimum of ten reseals*, enabling the end-user to use the original package for protecting the product inside rather than utilizing another container. This prolongs the use of one plastic package per product’s lifespan, which reduces overall plastic waste.
- Reduce overall material weight: Reseal packaging technology used with flexible, resealable lidding film can reduce plastic material weight by 30%* compared to fully rigid containers such as clamshells. By weighing less, more packaging material can fit in a single shipment, reducing overall carbon emissions.
- Improve recyclability: Further, a resealable lidding film can be used with recyclable APET trays, allowing the overall package to provide an improved environmental footprint.
Problem #1: Many Reseal Adhesives Cause Blushing
Unfortunately, blushing is a common problem with reseal adhesives in moisture-exposed food packaging applications, such as produce. Most reseal lidding films are clear to allow the end-user to see the product inside. However, most reseal adhesives used with these films will water whiten, which will create the blushing effect that prevents consumers from being able to see through the film. Blushing can also affect the graphic design if there is a logo or design on the film. While the package will still reseal, blushing creates optical problems that may result in an end-use thinking the product is no longer safe to use, which could hinder reseal packaging’s overall goal of reducing food waste.
The Right Reseal Adhesive Technology Mitigates Blushing
The first to the market for anti-blush reseal adhesives, our solvent-based solution offers robust performance against high moisture, providing reseal without water whitening. It also has FDA compliance for indirect food contact applications.
Along with a package that goes beyond one-time use, when a reseal adhesive offers anti-blush capabilities, it allows the end-user to easily see through the package to know whether a product, such as produce that involves moisture, is still fresh. This convenience will help an end-user keep the product throughout its true lifespan and reduce food waste.
A reseal adhesive with anti-blushing capabilities also enables you to:
The Right Reseal Adhesive Technology Mitigates Blushing
The first to the market for anti-blush reseal adhesives, our solvent-based solution offers robust performance against high moisture, providing reseal without water whitening. It also has FDA compliance for indirect food contact applications.
Along with a package that goes beyond one-time use, when a reseal adhesive offers anti-blush capabilities, it allows the end-user to easily see through the package to know whether a product, such as produce that involves moisture, is still fresh. This convenience will help an end-user keep the product throughout its true lifespan and reduce food waste.
A reseal adhesive with anti-blushing capabilities also enables you to:
- Use existing equipment: Even if you were previously using a waterborne reseal solution, this solvent reseal solution is compatible with standard coating equipment, allowing you to use your current manufacturing assets. Further, it is a coater-ready solution, allowing you to simplify your processes by eliminating steps to dilute or apply additives yourself.
- Simplify processes: Our reseal technology with anti-blush capabilities can still be used effectively for packaging that does not involve high moisture. By relying on one technology for all your reseal applications, you can reduce your overall SKU volume to simplify your processes.
Problem #2: Many Reseal Solutions Can’t be Used on All Packaging Structures
It’s likely that you are currently offering your brand owners coating capabilities if you own a coater and extrudable reseal options if you use extruders. Coating capabilities allow for die-cut flow wraps or lidding applications, while extrusion capabilities provide fully open lidding. However, if brand owners are looking for a packaging structure that you do not have the capabilities to process with your equipment, it may deter them from choosing you as the converter. This might lead you to consider investing in the equipment you do not currently own to offer the other capability, so that brand owners can rely on you for all their packaging needs. However, even if you do own both capabilities, you will still need to invest in separate reseal technologies, as extrusion and coating use different technologies.
The Right Reseal Adhesive Technology Works on All Structures
By choosing a reliable supplier with a portfolio of adhesive technologies, you will be able to provide brand owners with reseal packaging options regardless of whether you have coating or extrusion capabilities. This helps you avoid using valuable time to decide on multiple suppliers and allows you to communicate with one supplier for all your needs or questions. When deciding what reseal option is best for your business, consider:
The Right Reseal Adhesive Technology Works on All Structures
By choosing a reliable supplier with a portfolio of adhesive technologies, you will be able to provide brand owners with reseal packaging options regardless of whether you have coating or extrusion capabilities. This helps you avoid using valuable time to decide on multiple suppliers and allows you to communicate with one supplier for all your needs or questions. When deciding what reseal option is best for your business, consider:
- Water and solvent-based reseal coatings provide you with a press-ready solution to create die-cut reseal packages. These coatings allow for customization in coat weight to help achieve the desired peel strength when a consumer opens the package.
- M-resin reseal technology is based on extrudable, pressure sensitive adhesives. It is ideal for reseal lidding trays, including recyclable options, and is notable for its high peel strength. This technology is available in various adhesive formulations to address specific temperature and humidity needs. M-resins can be processed on standard multi-layer extrusion equipment, including blown and cast film lines.
How Bostik Can Help
Bostik’s reseal technology enables you to do more than reseal, offering:
Contact an Expert
*based on data from internal lab testing
- High end-use performance: From our anti-blushing reseal technology to m-resin adhesives, our team is continually developing new formulations that will address unmet needs in the market. Additionally, we can customize formulations to meet your specific needs.
- Efficient processes: With adhesive solutions for both die-cut reseal or flange seal tray reseal packaging, our coater-ready solutions allow you to rely on one supplier to simplify your processes. Bostik also has pilot capabilities to provide you the proof-of-concept prior to running on your production lines, helping reduce your costs.
- Enhanced sustainability: A study conducted with RecyClass has proven our adhesives do not contaminate the tray. Additionally, our m-resin reseal technology is certified as recyclable on PE film by RecyClass.
Contact an Expert
*based on data from internal lab testing
©2023 Bostik, Inc. All Rights Reserved
All information contained herein is believed to be accurate as of the date of publication, is provided “as-is” and is subject to change without notice. To review our full U.S. Legal Disclaimer, visit: https://bostik.com/us/en_US/privacy-policy/legal-disclaimer
All information contained herein is believed to be accurate as of the date of publication, is provided “as-is” and is subject to change without notice. To review our full U.S. Legal Disclaimer, visit: https://bostik.com/us/en_US/privacy-policy/legal-disclaimer